Custom plastic extrusion tailored to your industry needs
Custom plastic extrusion tailored to your industry needs
Blog Article
Secret Advantages and Factors To Consider of Executing Plastic Extrusion in Your Projects

Recognizing the Basics of Plastic Extrusion
Plastic extrusion, a staple in the production market, is a procedure that involves melting raw plastic product and improving it right into a continual profile. This account, once cooled down, can be cut into preferred sizes or coiled for later use. The appeal of plastic extrusion exists in its flexibility. A wide variety of items, from piping to window frameworks, can be created. The procedure calls for an extruder, an elaborate machine with a warmed barrel, a turning screw, and a die at the end. The plastic product, in the form of pellets, is fed right into the extruder, where it's melted and compelled through the die, taking its shape. The choice of plastic and the style of the die establish the product's qualities.
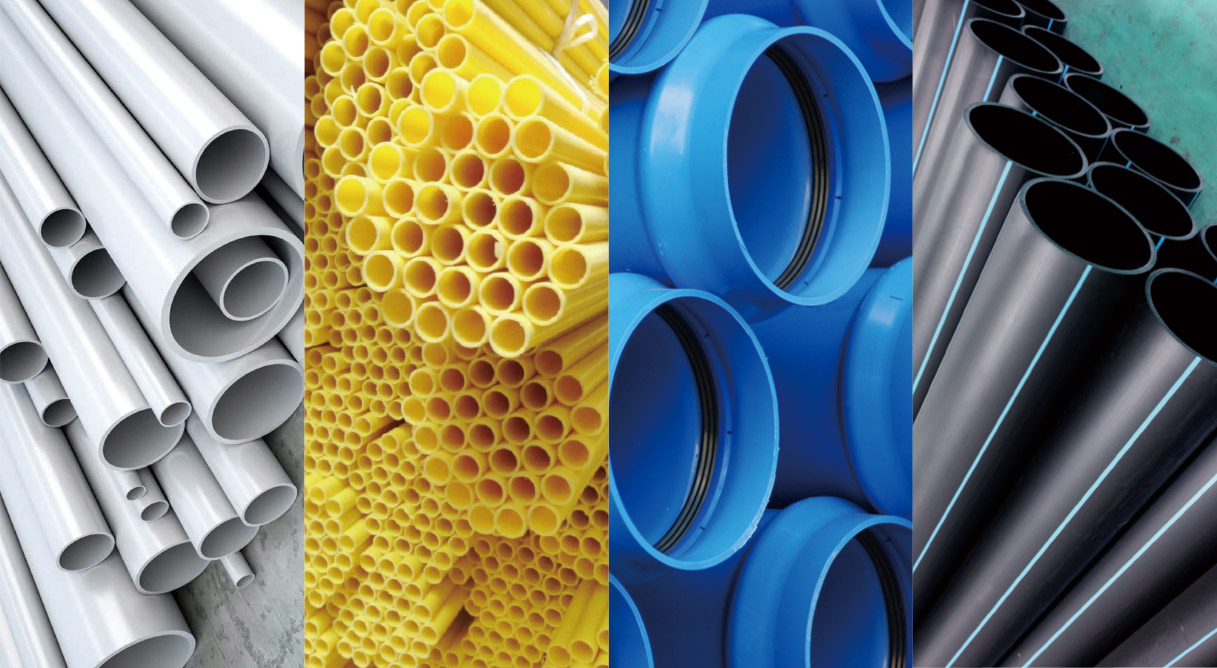
The Economic Benefit of Plastic Extrusion
The economic benefit of plastic extrusion lies mostly in two locations: economical material manufacturing and valuable production rates. With plastic extrusion, companies can produce high volumes of material at a reduced cost contrasted to other methods. In addition, the procedure boasts an outstanding manufacturing rate, substantially reducing time and additional enhancing its economic feasibility.
Cost-Effective Product Manufacturing
A substantial advantage of plastic extrusion is its exceptional cost-effectiveness. This manufacturing process enables continual, high-volume production with minimal waste, which equates into lower prices. The raw products made use of, normally plastic pellets, are reasonably affordable compared to other compounds (plastic extrusion). The process itself requires much less power than many other manufacturing techniques, better reducing prices. Furthermore, the extrusion procedure permits a high level of precision in forming the plastic, reducing the need for costly post-production changes or corrections. Furthermore, the sturdiness and long life of extruded plastic products commonly imply much less require for substitutes, contributing to lasting cost savings. All these aspects make plastic extrusion a very affordable choice for many tasks, supplying an eye-catching equilibrium in between expense and performance.
Beneficial Production Speeds
While preserving the cost-effectiveness of the materials, an additional noteworthy benefit of plastic extrusion exists in its fast manufacturing speeds. This performance in the manufacturing process is attributed to the continual nature of the extrusion procedure, permitting high-volume production in a relatively short time period. The speed of manufacturing directly correlates to a decline in labor prices and a rise in outcome, thereby boosting the general economic practicality of the procedure. The hectic manufacturing does not compromise the top quality of the last product, making sure dependable and regular results. This mix of high quality, cost-effectiveness, and rate highlights the substantial financial advantage of applying plastic extrusion in numerous jobs.
Adaptability and Customization: The Strengths of Plastic Extrusion
One of the famous staminas of plastic extrusion exists in its versatility and customization potential. These qualities open the door to limitless design possibilities, giving manufacturers the ability to customize items to certain requirements. This increased level of customization not just improves product capability yet likewise dramatically improves product individuality.
Endless Style Possibilities
Plastic extrusion radiates in its ability to offer almost endless design opportunities. This technique offers liberty to produce intricate accounts and complicated forms, a feat difficult to achieve with other manufacture methods. Owing to the liquid nature of molten plastic, the procedure is flexible enough to produce a diverse series of dimensions, dimensions, and kinds. The plastic can be adjusted to match distinct specifications, enabling the manufacturing of personalized geometries and meeting particular client demands. Plastic extrusion can take care of a selection of plastic kinds, expanding its application range. This versatile method, for that reason, offers a vast array of sectors from building to vehicle, packaging to electronics, and beyond. With plastic extrusion, the design possibilities are basically limitless.
Improving Item Originality
The versatility of plastic extrusion can significantly enhance product uniqueness. This process enables developers to try out different shapes, sizes, and shades, providing the flexibility to produce distinct products that attract attention on the market. It is this personalization that provides a distinct identification per item, differentiating it from its competitors.
In enhancement to its visual benefits, the customizability of plastic extrusion likewise offers practical benefits. Designers can modify the homes of the plastic according to the particular requirements of the application, boosting the product's functionality. For example, they can make the plastic much more flexible, extra long lasting, or much more resistant to heat, depending on what the item needs. Thus, plastic extrusion not just improves product originality but additionally its utility and marketability.
Layout Limitations in Plastic Extrusion: What You Need to Know
Exactly how can design constraints potentially impact the procedure of plastic extrusion? While plastic extrusion is flexible, layout restrictions can cut its advantages. Particular complicated layouts might not be possible due to the restrictions of the extrusion procedure, possibly restricting the creation of complex accounts. The procedure is less ideal for multi-chambered or hollow frameworks. Additionally, the extrusion process may not constantly check my blog provide the desired surface coating, especially for those calling for high gloss or optical clarity. Material selection can additionally posture difficulties, as not all polymers appropriate for extrusion. High-temperature resistant plastics, for instance, may provide problems. Recognizing these restrictions is crucial for effective application of plastic extrusion in your jobs. plastic extrusion.
Assessing the Environmental Impact of Plastic Extrusion
While understanding style constraints is a considerable element of plastic extrusion, it is equally vital to consider its ecological effects. The procedure of plastic extrusion involves melting plastic products, possibly releasing hazardous gases into the find out this here setting. Even more, the resulting products are often non-biodegradable, adding to garbage dump waste. Nonetheless, innovations in innovation have enabled more environmentally-friendly techniques. Utilizing recycled plastic products in the extrusion process can reduce ecological impact. In addition, establishing biodegradable plastic options can help alleviate waste concerns. Examining these environmental elements is crucial when executing plastic extrusion projects, guaranteeing an equilibrium between performance, cost-effectiveness, and ecological responsibility.
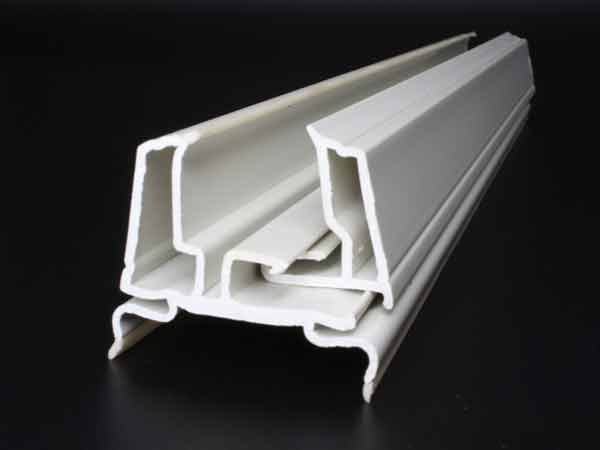
Study: Successful Projects Using Plastic Extrusion
Success tales in the field of plastic extrusion abound, demonstrating both the versatility and effectiveness of this manufacturing procedure. plastic extrusion. An additional effective situation is the production of plastic movie for packaging and agriculture. These circumstances highlight plastic extrusion's critical role in numerous fields, proving to its flexibility, cost-effectiveness, and trusted output.
Conclusion
Finally, plastic extrusion supplies a affordable and effective technique for producing intricate forms with minimal waste. While it provides countless advantages such as cost-effectiveness and flexibility, it's vital to take into consideration prospective design constraints and environmental impacts. Executing eco-friendly or recycled materials can mitigate these issues, enhancing sustainability. Integrating plastic extrusion into jobs can lead to successful end results, as confirmed by countless study.
Plastic extrusion, a staple in the production industry, is a process that involves melting raw plastic product and improving it into a constant account. Plastic extrusion can manage a selection of plastic types, broadening its application range.Just how can make limitations potentially impact the pop over to this web-site procedure of plastic extrusion? The procedure of plastic extrusion entails melting plastic products, potentially releasing damaging gases into the setting. Making use of recycled plastic products in the extrusion procedure can reduce ecological impact.
Report this page